No products in the cart.
Best Micro Concrete Solution for Durable and Precise Repairs
Micro concrete also known as micro cement or micro-topping, is a type of thin cementitious coating that is applied to various surfaces to create a smooth and durable finish. It is commonly used in interior and exterior design applications, including floors, walls, countertops, and furniture.
Here are some key characteristics and features of micro concrete:
- Thickness: This is typically applied in thin layers, ranging from 2 to 4 millimeters in thickness. This allows it to be used as an overlay on existing surfaces without significantly raising the floor or wall level.
- Composition: This is composed of a blend of cement, fine aggregates, polymers, and additives. This combination creates a highly adhesive material those bonds well with different substrates.
- Appearance: It’s provides a seamless and continuous surface, offering a sleek and modern aesthetic. It is available in a wide range of colors, allowing for customization and creative design options.
- Durability: Despite its thin application, micro concrete is known for its durability and resistance to wear, abrasion, and impact. It forms a hard and compact surface that can withstand heavy foot traffic and general use.
- Waterproofing: Micro concrete is often applied with a protective sealer, which enhances its water resistance and makes it suitable for wet areas such as bathrooms, kitchens, and showers.
- Versatility: Micro concrete can be used on various substrates, including concrete, wood, tiles, and even metal. This versatility makes it a popular choice for both new construction projects and renovation work.
- Application process: The application of micro concrete involves several steps, including surface preparation, primer application, and the actual coating of micro concrete layers. Skilled professionals usually perform the installation to ensure a high-quality and flawless finish.
- Maintenance: Proper maintenance is essential to prolong the lifespan of micro concrete. Regular cleaning with pH-neutral detergents and periodic resealing can help maintain its appearance and protect it from stains and damage.
It’s worth noting that while micro concrete shares similarities with other cementitious coatings like micro cement and polished concrete, there may be slight differences in terms of composition and application techniques depending on the specific product and manufacturer.
Micro concrete mix ratio:
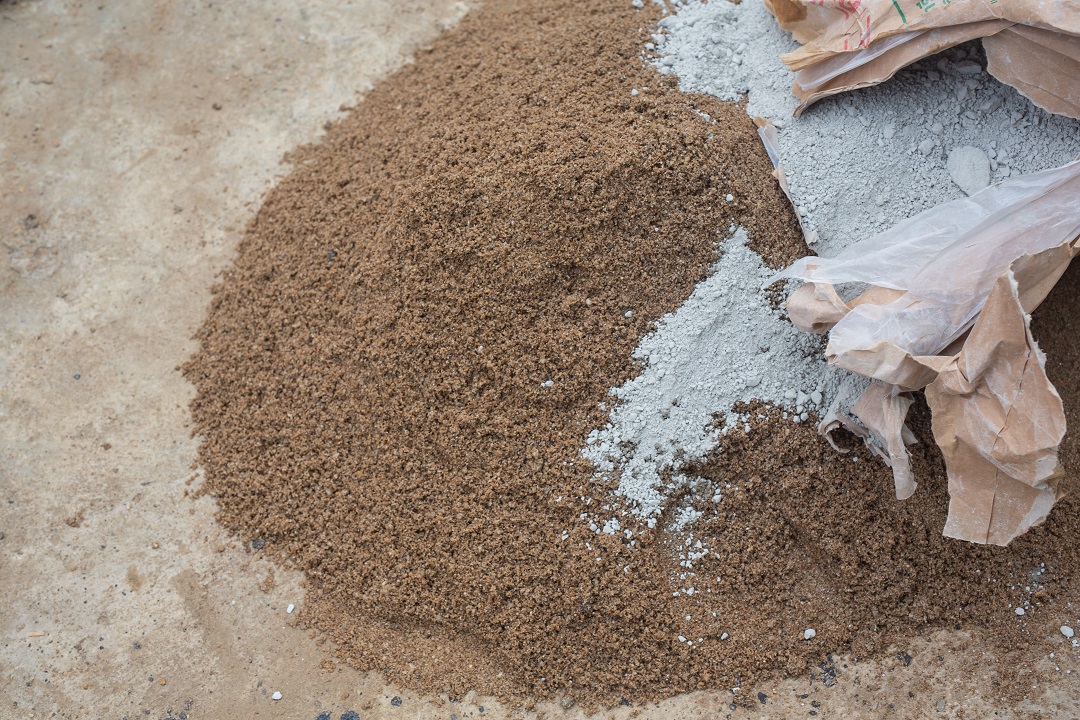
The mix ratio for micro concrete can vary depending on the specific application and desired strength. However, a commonly used mix ratio for micro concrete is:
- Cement: Sand: Water = 1:2:0.5
This means that for every part of cement, you would use two parts of sand and 0.5 parts of water.
It’s important to note that this ratio is just a general guideline and can be adjusted based on factors such as the desired strength, aggregate size, and other additives used in the mix. It’s always recommended to refer to the manufacturer’s instructions or consult with a concrete expert for specific projects to ensure the best results.
Micro concrete texture:
Micro concrete texture refers to the surface finish or pattern created on a micro concrete surface. It’s also known as micro-topping or skim coat is a thin layer of concrete typically applied to existing surfaces such as floors, walls, or countertops to achieve a decorative and durable finish.
The texture of micro concrete can vary depending on the desired aesthetic effect. Here are a few common micro concrete textures:
- Smooth Texture: This texture is achieved by applying the micro concrete mixture evenly and then toweling it to create a smooth and polished surface. It gives a smooth & contemporary look.
- Trowel Texture: By using a trowel, the micro concrete can be manipulated to create various patterns and textures. The trowel marks add subtle variations and a slightly rougher finish.
- Stamped Texture: This texture is achieved by pressing stamps or templates into the micro concrete surface while it is still wet. Stamps can mimic the appearance of materials like stone, brick, or wood, creating a textured and realistic finish.
- Stenciled Texture: Stencils can be used to create intricate patterns on the micro concrete surface. The stencil is laid on the wet micro concrete, and a trowel or a roller is used to apply a contrasting color or texture. When the stencil textures are removed, the pattern will remain.
- Exposed Aggregate Texture: This texture is achieved by incorporating decorative aggregates, such as small stones or glass chips, into the micro concrete mix. Once the surface is troweled and cured, the aggregates are partially exposed, creating a textured and decorative finish.
- Burnished Texture: This texture is created by using a burnishing tool, such as a power trowel or a burnishing pad, to polish the micro concrete surface. It results in a smooth and glossy finish with a subtle sheen.
These are just a few examples of textures that can be achieved with micro concrete. The choice of texture depends on the desired aesthetic, functionality, and techniques employed during the application process.
Micro concrete specifications:
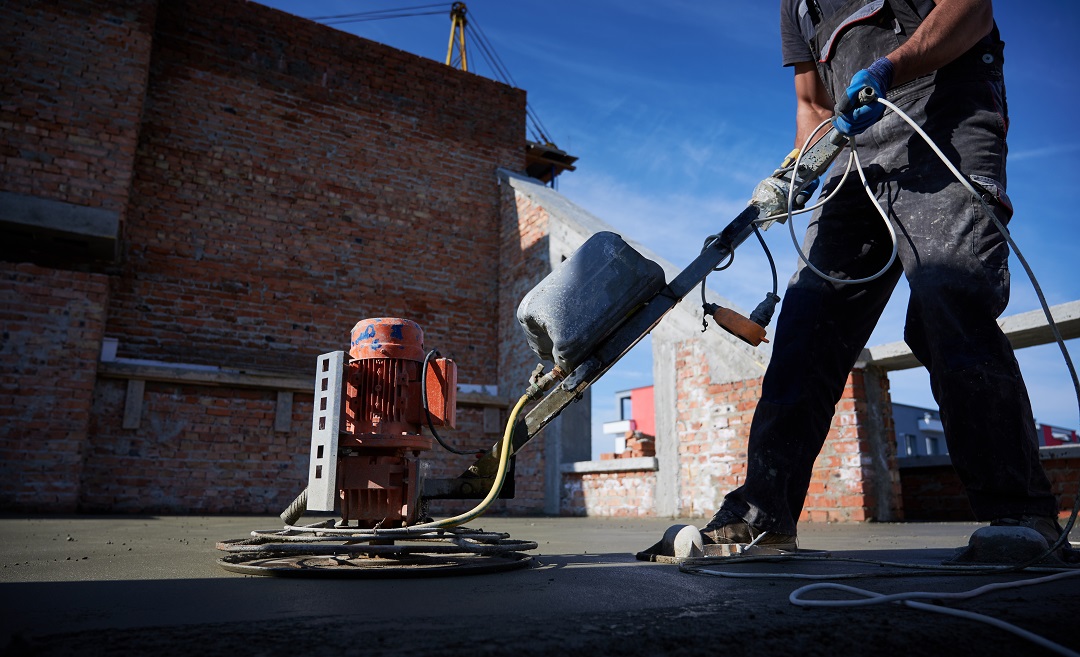
- Composition: It is typically a blend of Portland cement, fine aggregates (such as silica sand or quartz), polymers, and additives. The exact composition may vary depending on the manufacturer and specific product.
- Thickness: Micro concrete is applied in thin layers, usually ranging from 1 to 3 millimeters. However, the thickness can vary based on the desired effect and application requirements.
- Surface preparation: The substrate or surface where micro concrete will be applied should be properly prepared. This usually involves cleaning the surface, repairing any cracks or imperfections, and ensuring it is stable and free from dust, grease, or other contaminants.
- Application method: It can be applied by troweling, spraying, or rolling, depending on the manufacturer’s recommendations and the desired finish. It’s necessary to follow the manufacturer’s instructions for proper application techniques.
- Curing: After application, micro concrete needs sufficient time to cure and harden. The curing time can vary but is typically around 24 to 48 hours. During this period, it’s crucial to protect the surface from moisture and physical damage.
- Finishing: It can be finished in various ways, such as polishing, burnishing, or applying a protective sealer. The desired aesthetic and functional requirements will determine the appropriate finishing techniques.
- Colors and patterns: Micro concrete is available in a wide range of colors, allowing for versatile design possibilities. It can also be used to create patterns, textures, or even mimic the appearance of other materials like stone or marble.
It’s important to note that these specifications can vary depending on the specific product and manufacturer. Therefore, it’s always recommended to refer to the manufacturer’s technical data sheet and follow their guidelines for the particular micro concrete product you are using.
Micro concrete application:
This is a high-performance, fiber-reinforced cementitious material that is commonly used for repair and rehabilitation applications. It is characterized by its high strength, durability, and excellent bond strength with existing concrete surfaces. Here are some common applications of micro concrete:
- Structural Repairs: It’s often used for structural repairs in buildings, bridges, and other infrastructure. It can be applied to repair damaged concrete elements such as columns, beams, slabs, and walls. It can effectively restore the load-bearing capacity and structural integrity of deteriorated or damaged structures.
- Joint and Crack Repairs: It’s used to repair joints and cracks in concrete surfaces. It can be applied to fill and seal cracks, preventing the ingress of water, chemicals, and other contaminants. Micro-concrete has good flowability, allowing it to penetrate and bond well with the existing concrete substrate.
- Spall and Patch Repairs: Micro-concrete is ideal for repairing spalled or deteriorated concrete surfaces. It can be used to fill voids, repair surface defects, and restore the appearance of concrete elements. Micro-concrete can be applied as thin overlays or patches, providing a smooth and durable surface finish.
- Anchoring and Grouting: This is commonly used for anchoring and grouting applications. It is used to fix anchor bolts, dowels, and other embedded elements in concrete or masonry. It’s provides excellent load transfer and bond strength, ensuring secure and long-lasting connections.
- Precast Elements: It is also used in the production of precast concrete elements. It is often used as a self-compacting concrete to fill intricate molds and achieve high-quality finishes. It’s high strength and durability make it suitable for various precast applications such as architectural elements, façade panels, and decorative elements.
- Flooring and Topping: It can be used as a topping material for floors, providing a durable and abrasion-resistant surface. It is commonly used in industrial settings, warehouses, and commercial spaces where high traffic and heavy loads are expected. M-C toppings can be applied in thin layers, providing a smooth and level finish.
It’s important to note that the specific application and design considerations may vary depending on the project requirements. It is recommended to consult with a qualified engineer or contractor who has experience in working with micro concrete to ensure proper application and adherence to relevant standards and guidelines.